Innovative Technologies for Cooling, Process and Boiler Water Treatment
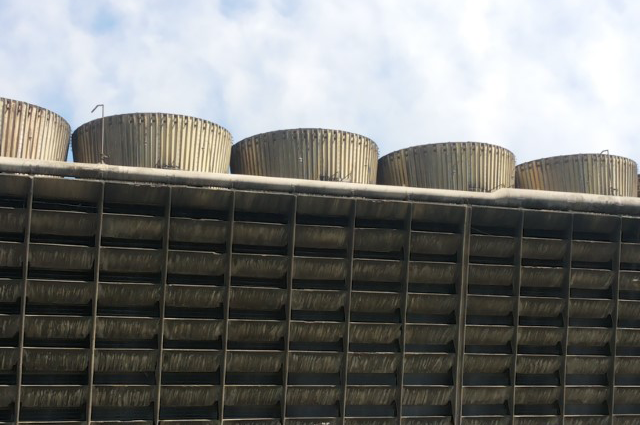
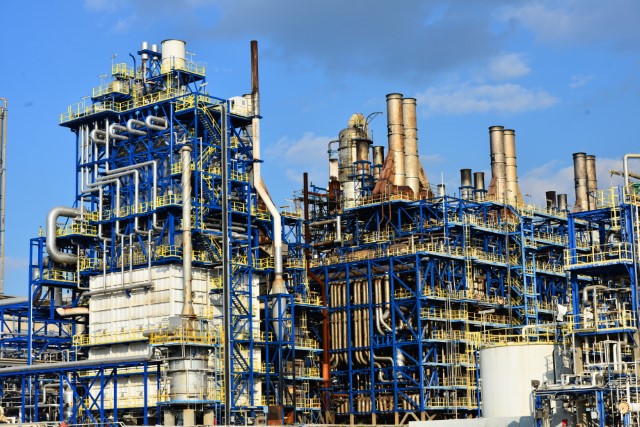
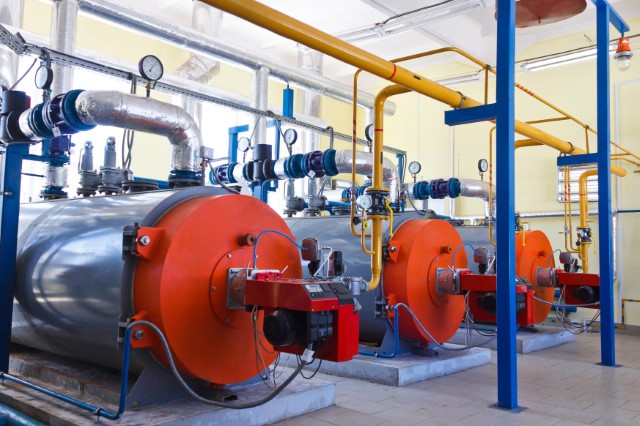
Cooling Water
Corrsave® 100 Technology
Environmentally friendly newly developed active Corrosion Inhibitor and its product range.
For active corrosion inhibition there only where two choices: Low corrosion rates with high Phosphate content or high corrosion rates with low phosphate content.
Corrsave® exactly has been developed to fill this Gap: Low corrosion rates with low Phosphate content. Depending on the chosen treatment approach the absolute level may vary, however with its product range Corrsave® 100 technology can reduce P intake for all organic treatment concepts as well as for traditional Phosphate based treatments.
Products based on Corrsave® 100 technology combines already two aspects inherently biodegredable and reducing significantly the Phosphate (or Zinc) demand but is providing active corrosion and pitting inhibition.
Within this respect specialized products with Corrsave® 100 technology product range has been set up to cover different requirements:
- Aktiphos CS 4170 is the product of choice for treatment without pH control (so called all organic treatment).
- Aktiphos CS 4180 makes Corrsave® 100 technology in soft water systems.
- Aktiphos CS 4060 completes the range with active anodic and cathodic corrosion protection for very corrosive waters.
FReE
Like in daily live dust and contamination can occur occasionally, of course everybody tries to avoid as much as possible. However sometimes it is not. Dust and other materials can easily enter through the cooling air. Therefore, it is important to clean the system regularly to FReE it from fouling and other contaminations.
Also, Kurita’s FReE technology offers adaption to various situations. The basis treatment is the combined fouling removal and azole free Copper Inhibitor Turbodispin 4363.
It can be used alone (for organic removal) in combination with any other Kurita water treatment program, or in combination
If Turbodispin 4363 is combined with Kurita’s own range of Turbodispin D -Polymers a system online cleaning can be performed suitable to remove organic and inorganic deposits that have accumulated in the system.
A further most important step for smooth trouble-free system operation is the cleanliness of the system.
Turbodsipin D – Polymers
To be able to have polymers especially designed to meet water treatment needs, Kurita uses its own developed polymers rather than commonly available multi use polymers.
This enables Kurita to set up products with exactly tailored polymers for local water quality.
360º
Applied together Corrsave®, FReE and Turbodispin D Polymers provides a 360° treatment concept for your Cooling System 365 days/year.
Process
Kurita's ACF Technology
Fouling and corrosion prevention
Kurita’s globally proven ACF Technology offers the possibility to prevent ammonium salt fouling during production and to avoid or at least significantly reduce the risk of chloride corrosion. With Kurita´s ACF Technology you benefit from:
- Prevention of salt fouling and corrosion by forming liquid ACF salts. These salts have a neutral pH and very low corrosion potential.
- Removal of already formed ammonium salt deposits during operation.
- Immediate reaction with very corrosive hydrochloric acid and ammonium salts.
- Formed ACF salts can be easily removed with wash water or sour water. Liquid ACF salts are hygroscopic and have a very low corrosion potential.
- Ensures a long lifetime of the process equipment.
- Reduces the need for cleaning operations.
Kurita Cleaning & Decontamination
Kurita’s cleaning and degassing programs reduce the necessary cleaning times and ensure safe working conditions. The handling of our cleaning and decontamination additives is easy and safe for the operating personnel.
A mechanical cleaning and decontamination of storage tanks may require several weeks of downtime. In comparison, the chemical cleaning and degassing will reduce the downtime significantly to a few days providing a great economic advantage. Less labour intensive work compared to mechanical cleaning will be required.
Packinox plate heat exchangers or Texas Tower tubular heat exchangers require more cleaning efforts than classical heat exchangers. Kurita´s cleaning concepts are the method of choice when Packinox heat exchangers or Texas Towers need to be cleaned.
Kurita Corrosion Control
Corrosion attack is an omnipresent threat to oil refineries and petrochemical plants.
Film-forming amines are the most common corrosion inhibitors. They form a protective layer on the metal surface. This results in a better corrosion protection by increasing the corrosion resistance.
Oil soluble filming amines are well established in oil refineries and petrochemical plants. They need hydrocarbons from the process stream to form a protection layer. They are used in hydrocarbon systems with lower water content. Process systems with high water content are vacuum overheads, sour water strippers, water quench columns or amine units.
Water-soluble filming amines offer excellent corrosion protection properties. Kurita provides high-performing oil soluble and water soluble amine for corrosion protection. Kurita´s modern neutralising amine blends provide excellent corrosion protection and very good buffering capacities. They operate by reacting with any acid constituent in a straight forward chemical neutralization. The neutralising amine shifts the pH from very corrosive conditions to levels which are easier to control. They demonstrate an easier pH control and better handling.
Related Articles
- PTQ 2021 - Managing ammonium salts corrosion and fouling
- Hydrocarbon Engineering 2021 - Away with the Salts
- Hydrocarbon Engineering 2019 - Caustic replacement
- PTQ 2018 - Maximising heat exchanger cleaning
- PTQ 2017 - Preventing ammonium salt fouling and corrosion
- Hydrocarbon Engineering 2017 - Curtailing contamination
Boiler
Cetamine® Technology
Excellent protection against corrosion in boiler systems, steam generators and closed systems.
Based on surface-active film-forming substances a protective Cetamine®-film is formed on all system surfaces.
Compared to traditional treatment programs where up to 3 different products are necessary the application of Kurita’s Cetamine® Technology usually requires one product only to treat the whole plant. Existing scale is removed from system surfaces during normal operation and the formation of new scale is prevented.
As an all-organic treatment program Cetamine® allows:
- Optimized blow-down rates with higher cycles of concentration,
- Significant lower fresh make-up water consumption,
- Savings in energy,
- Reduction of CO2 emission.
The active components of Cetamine® products are volatile and protect the whole water/steam cycle. Investigations in a triple pressure Heat Recovery Steam Generator (HRSG) proved the presence of the protective Cetamine®-film both water and steam touched surfaces including high-pressure evaporators, reheaters, and low-pressure turbine cylinders.
Kurita’s Cetamine® Wipe Test
To demonstrate the presence of the protective Cetamine®-film on system surfaces Kurita’s Cetamine® Wipe Test can be applied on accessible system surfaces during routine plant inspections. This is a semi-quantitative method to transfer the FFA molecules from a defined system surface into a liquid solution. Once the molecules have been transferred, they can be analysed with the Cetamine® Photometric Method.