Meeting the demands of a changing energy landscape
The energy sector is undergoing a fundamental transformation with power plants required to operate flexibly with frequent start-ups, shutdowns and preservation periods. These demanding conditions have made traditional water-steam cycle treatments insufficient.
Kurita’s Cetamine® Technology, based on Film Forming Amines, addresses this challenge by providing advanced corrosion protection specifically for cycling and intermittent plant operation.
This innovative treatment integrates with existing chemical programs. As a result, operators benefit from improved system protection, reduced turbine coupling times and improved water and energy efficiency.
Technology Features and Benefits
Cetamine G85X
- Patented technology
- Film-forming corrosion inhibitor
- Single component without stabilizer
- Ideal distribution between liquid and steam phase
- Protection of all ferrous and mixed metallurgy systems
Performance improvement
- Reduction of corrosion and metal oxide transport in intermittent and stop-start operations
- Corrosion protection even during shutdowns under wet and dry conditions
- Lower total Fe during start-up conditions
- Faster start-up and turbine coupling times
- Reliable unit availability
Compliance & Compatibility
- Degassed Cation Conductivity in accordance with international guidelines
- Easy integration with existing chemical treatment programs under AVT(O) and AVT(R) conditions
- Compatible with online sensors and Condensate Polishing Units
- Listed in IAPWS Technical Guidance Documents (TGD 8-16, 11-19) for safe and effective use in steam generators
Flow-accelerated corrosion (FAC) mitigation
- Single phase FAC
- Two phase FAC
Sustainability Impact
- Lower environmental footprint
- Energy & water efficiency
- Reduced operational costs
Enhancing Steam Cycle Reliability with Cetamine® in Intermittently Operating Power Plants
Cetamine® is Kurita’s patented corrosion inhibitor designed for intermittently operating power plants. It forms a protective film in the water-steam cycle, mitigating flow-accelerated corrosion (FAC) and safeguarding systems with ferrous and mixed metallurgy components.
Plant operators benefit from reduced iron oxide transport during cycling and stop-start operations, enabling faster start-ups and shorter turbine coupling times.
Widely used in plants that experience frequent shutdowns and start-ups, Cetamine® is an ideal solution for both wet and dry lay-up preservation. After implementation, plants retain full operational flexibility without compromising steam quality.
Cetamine® consistently delivers significantly lower total iron levels during start-up compared to conventional treatments such as AVT(O) or AVT(R). This improvement often enables reduced blow-down rates, leading to measurable savings in water and energy consumption. In turn, this lowers the environmental footprint and supports power producers in achieving their sustainability goals.
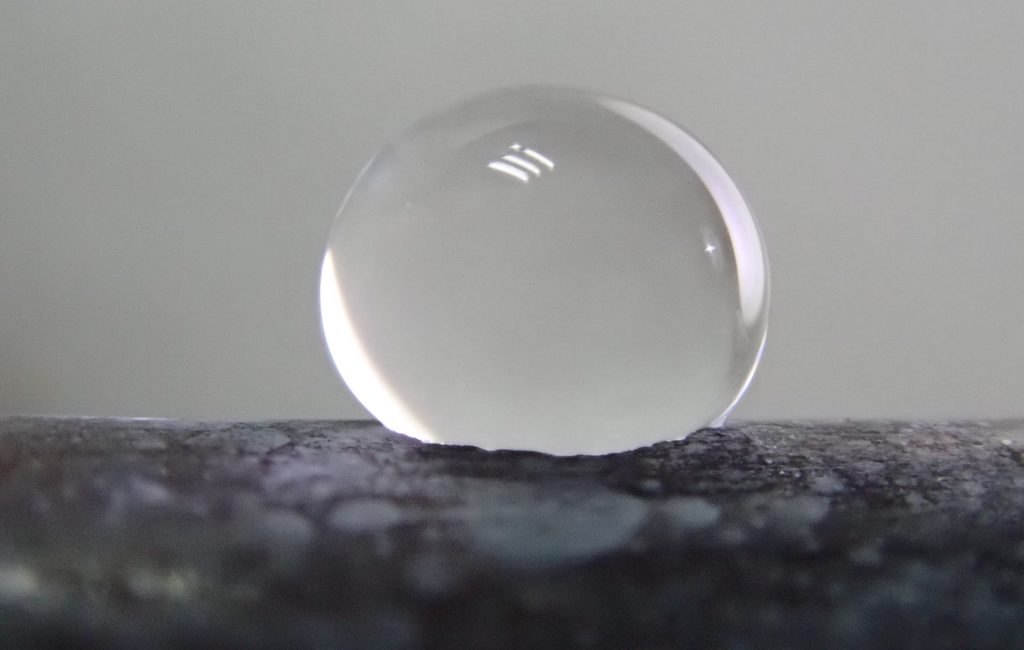
Customer Testimonial
1) Ideal distribution of active components in the whole network resulting in optimal alkalization.
2) Excellent protection against corrosion.
3) Economical savings in terms of lower product consumption.
4) Full technical support for the treatment concept implementation.
5) Implementation of a non-toxic treatment program free of cyclohexylamine CPCU is entirely satisfied with Kurita’s Cetamine Technology and recommends its usage for boiler networks.
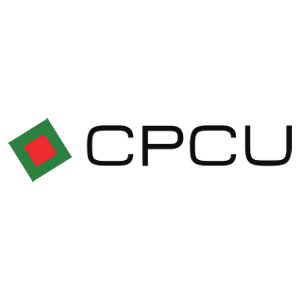
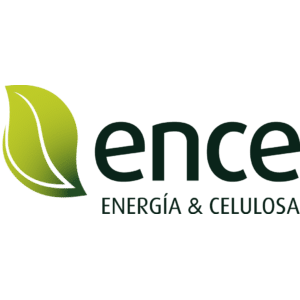
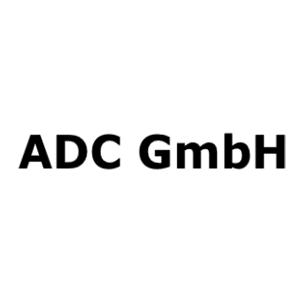
1) Heat Recovery Steam Generators and steam turbine internal surfaces are clean and free of corrosion.
2) Protection of components throughout the water steam cycle, including areas that could not be preserved by conventional preservation methods.
3) Reduced manpower for preservation tasks.
4) A reliable photometric method was provided by Kurita to monitor the residual concentration of Cetamine in water and steam samples.
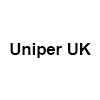