Steel production relies on vast amounts of water for cooling and gas scrubbing in processes like blast furnaces, converters, and strip mills. Modern steel plants have reduced freshwater usage through recycling and process optimization, yet water quality and wastewater regulations remain rigorous.
Kurita delivers specialized water treatment solutions tailored to the steel industry, addressing common issues such as corrosion, scaling, biofouling, and nozzle clogging. Enhance efficiency and comply with standards using our proven expertise.
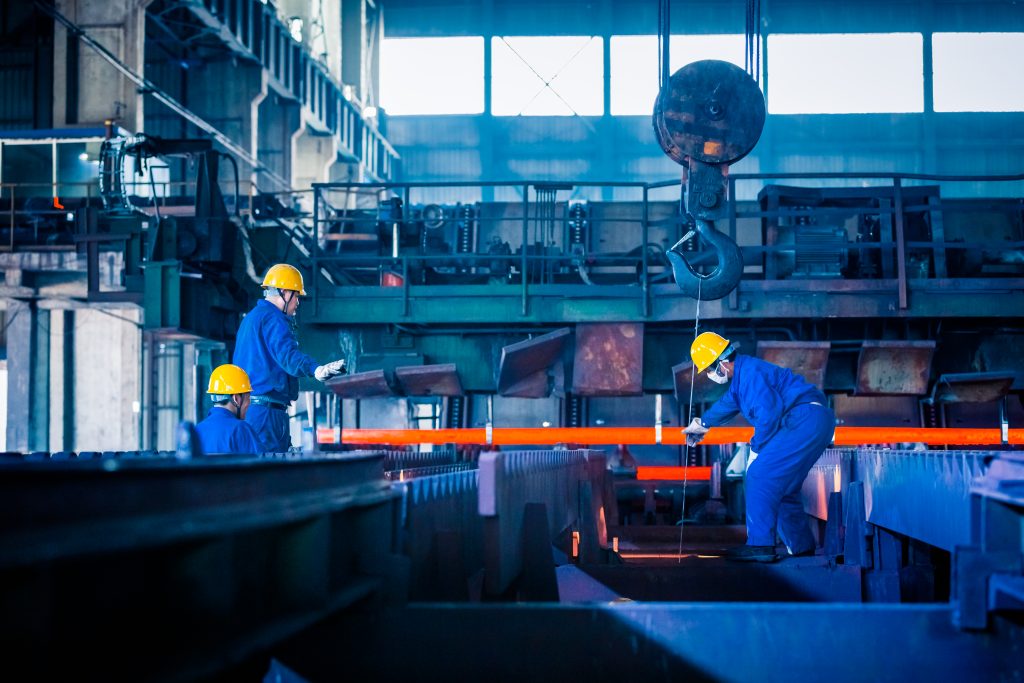
Industry Benefits at a Glance
Reduce operation cost
Improving raw material handling
Increase plant productivity
Maximize plant life cycle
Optimize plant & occupational safety
Steel Plants Process Flow and Solutions
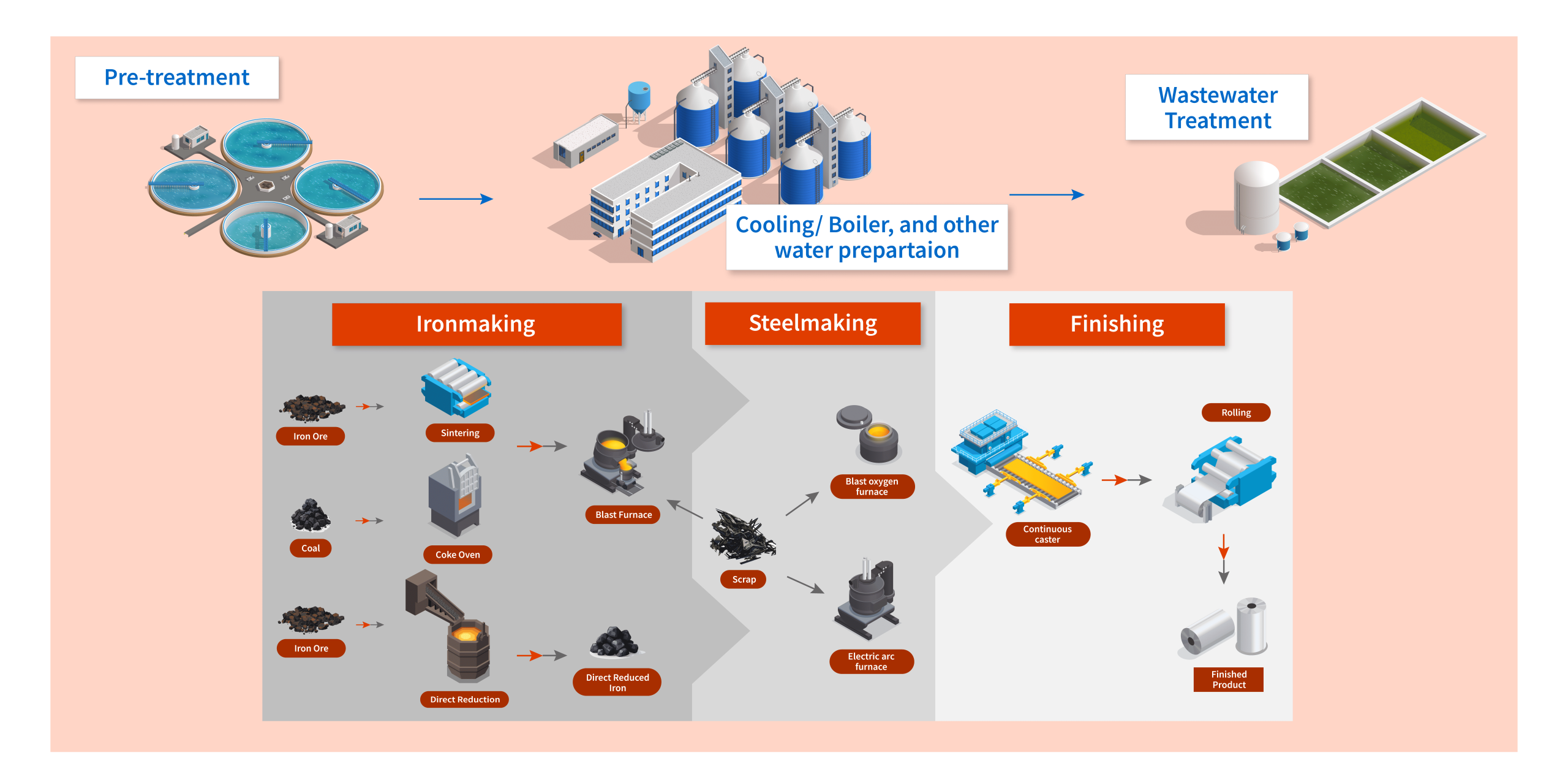
Raw Material Transport & Yard
Ferrosolf® product line provides a range of dust control, freeze prevention, and bulk material handling solutions aimed at meeting environmental regulations, ensuring employee safety, and optimizing bulk material throughput. Our extensive product lineup features foaming agents, pile sealants, handling improvers and road dust treatments. Our FFE units ensure the needed foam applications in dust control applications.
Sinter Plant and Burden Preparation
Optimization of the sintering process can be managed with proper and efficient chemical treatment.
Ferrosolf® product line and the FFE units provide the state of the art dust control, anticlogging and handling programms.
Coke Oven Plant
Kurita provides a comprehensive portfolio for Coke Oven plants, addressing water and process treatment needs across Oven, Gas and Water Treatment Plant operations. Our portfolio includes solutions for reverse osmosis, boiler and cooling systems to emulsion breakers for tar separation, and sealants for coke oven doors and caps.
Direct Reduction & Blast Furnace
Kurita delivers effective solutions for managing essential operational components, including process gas scrubbers, cooling gas scrubbers, clarifiers, and open- and closed cooling systems. By combining our comprehensive chemistry and service portfolio with innovative technologies, we ensure optimal performance for DRI plant water circuits, bringing significant value to our customers.
BOF and secondary Metallurgy
- Cetamine®, Aktiphos®, Ferrofos®, and Kuriflock® technologies ensure smooth operations with corrosion prevention and antiscalant benefits.
- Our membrane technologies provide local support to enhance system performance and include a variety of treatment solutions, such as chemicals, equipment, and services.
Electric Arc Furnace
- Cetamine®, Aktiphos®, Ferrofos®, and Kuriflock® technologies ensure smooth operations with corrosion prevention and antiscalant benefits.
- Our Avista membrane technologies provide local support to enhance system performance and include a variety of treatment solutions, such as chemicals, equipment, and services.
Continuous Casting
- The Ferrofos® program is designed to prevent nozzle clogging in spray water systems. This innovative solution ensures smooth operation and enhances the efficiency and reliability of the system.
- Cetamine® Technology provides excellent protection against corrosion and scaling in boiler and hot water systems.
- Kuriflock® polymers effectively reduce suspended solids, ensuring optimal filter and clarifier operation.
Hot and Cold Rolling
- Cetamine®, Aktiphos, Ferrofos, and Kuriflock technologies ensure smooth operations with corrosion prevention and antiscalant benefits.
- Dilurit® BC-S is a cutting-edge biocide designed for cooling water systems with high oil or suspended solids. It outperforms traditional biocides like chlorine dioxide, providing superior results in challenging conditions.
Finishing Lines
- The Ferrofos® program is designed to prevent nozzle clogging in spray water systems. This innovative solution ensures smooth operation and enhances the efficiency and reliability of the system.
- Cetamine® Technology provides excellent protection against corrosion and scaling in boiler and hot water systems.
- Dilurit® BC-S is a cutting-edge biocide designed for cooling water systems with high oil or suspended solids. It outperforms traditional biocides like chlorine dioxide, providing superior results in challenging conditions.
Water pre-treatment:
- Kuriflock® polymers effectively reduce suspended solids, ensuring optimal filter and clarifier operation.
- S.sensingTM CS technology uses laser-based equipment to control product dosage in industrial wastewater treatment. It allows precise dosage control at the sedimentation basin inlet and therefore savings in chemicals and reduction of TCO
- Kurita's membrane technologies enhance system performance and include a variety of treatment solutions, such as chemicals, equipment, and services.
- Ferrolin® cleaners to improve filter performance.
Cooling and Boiler Water Treatment:
- Kuriflock® polymers effectively reduce suspended solids, ensuring optimal filter and clarifier operation.
- Highly concentrated cooling water inhibitors for dispersing, stabilization, and corrosion inhibition in the Aktiphos® and Ferrofos® product lines, ensuring safe operation of cooling water systems.
- Dilurit BC-S is an advanced biocide designed for cooling water systems with high oil or suspended solids. It outperforms traditional biocides like chlorine dioxide, ensuring optimal results in tough conditions.
- Cetamine® Technology provides excellent protection against corrosion in closed cooling water and boiler systems.
- Kurita Connect360 is our digital customer platform developed for global water system management.
Wastewater Treatment:
- Kuriflock polymers reduce suspended solids for better filter and clarifier operation.
- S.sensing™ CS technology uses laser-based equipment for precise product dosage in wastewater treatment, optimizing chemical use and cutting total costs.
- Kurita offers membrane system local support with Avista™ Membrane Technologies
- Heavy metal and anion scavengers effectively remove contaminants like Zn, Cr, Pb, Hg, Ni, fluorides, sulfates, and phosphates across a wide pH range.
- Ferrolin® cleaners improve filter performance.
Key Technologies and Applications
Kurita provides a range of dust control, freeze prevention, and bulk material handling solutions aimed at meeting environmental regulations, ensuring employee safety, and optimizing bulk material throughput. Our extensive product lineup features foaming agents, pile sealants, handling improvers and road dust treatments.
Kurita offers an extensive portfolio for sinter plants, encompassing various aspects such as water treatment, process chemicals, and dust control. Our solutions include advanced dust control measures, efficient cooling water systems, and optimized scrubber operations. Additionally, we focus on enhancing sinter parameters to ensure optimal performance and efficiency in your operations.
Kurita’s proven treatment concepts for cooling water systems include local service, system-specific product application, and continuous customer support. Our products, developed through extensive research, meet state-of-the-art standards and focus on eco-friendly treatments such as AOX-free biocides and phosphate-free solutions.
- Cetamine® Technology provides excellent protection against corrosion and scaling in boiler and hot water systems.
- Ferrosolf® 8988, Ferrosolf® 8989 and Ferrosolf®9751 cap and door sealant mixes are operator-friendly, reduce dust, and enhance work safety on the oven top.
- Our range of process chemicals, including emulsion breakers for tar separation, antifoulants, and anticorrosion inhibitors for coke oven gas lines, is available through our EB, AP, and CI product lines.
- Kurita offers innovative AvistaTM membrane treatment solutions, including chemicals, equipment, and services designed to improve system performance and reliability.
Kurita delivers effective solutions for managing essential operational components, including process gas scrubbers, cooling gas scrubbers, clarifiers, and open- and closed cooling systems.
- Cetamine® Technology provides excellent protection against corrosion in closed cooling water systems.
- State-of-the-art cooling water inhibitors from the Aktiphos® and Ferrofos® product lines ensure safe operation of cooling water and gas scrubber systems. Kuriflock® polymers provide an effective solution for clarifier operation and reducing suspended solids.
- Kurita offers innovative membrane treatment solutions, including chemicals, equipment, and services designed to improve system performance and reliability.
Kurita provides effective solutions for managing essential operational components such as process gas scrubbers, cooling gas scrubbers, clarifiers, and both open and closed cooling systems. By integrating our extensive chemistry and service portfolio with innovative technologies, we ensure optimal performance for water circuits in Basic Oxygen Furnaces (BOF) and secondary metallurgical plants, delivering significant value to our customers.
Ensuring the reliable and consistent operation of the electric arc furnace (EAF) is essential for meeting downstream demand and cost targets. Key issues include mixed metallurgy, fouling, corrosion, and scaling, all intensified by high heat flux and cyclical operations. Kurita’s water treatment portfolio is designed to address these challenges comprehensively, ensuring optimal performance and minimizing disruptions.
Kurita provides effective solutions for managing Continuous Casting operations, including spray water systems, as well as open and closed cooling systems. By integrating our extensive chemistry and service portfolio with cutting-edge technologies, we ensure optimal performance for Continuous Casting water circuits, delivering substantial value to our customers.
To maximize throughput and maintain the availability of your rolling mill, Kurita offers a range of products. These products ensure clean heat exchange surfaces in the reheating furnace. Additionally, they help minimize scaling, corrosion, and clogging in milling stands. Furthermore, they maintain optimal clearwater quality after sedimentation basins or thickeners. By addressing these critical areas, Kurita’s solutions contribute to the efficient and reliable operation of your rolling mill.
Kurita’s treatment concepts for finishing lines, cooling, and boiler water systems include local service, tailored product applications, and continuous support. Our eco-friendly products, developed through extensive research, meet state-of-the-art standards, featuring AOX-free biocides and phosphate-free solutions.
Kurita offers a comprehensive program for clean make-up water, which includes solutions ranging from basic clarification to advanced processes like ultrafiltration and reverse osmosis. This approach ensures water quality meets operational standards, improving both efficiency and reliability.
Kurita’s proven treatment concepts for cooling water systems include local service, system-specific product application, and continuous customer support. Our products, developed through extensive research, meet state-of-the-art standards and focus on eco-friendly treatments such as AOX-free biocides and phosphate-free solutions.
The steel industry consumes large quantities of water and generates significant wastewater. To address environmental concerns and comply with regulations, these companies operate wastewater treatment plants. Kurita offers products and solutions to enhance water quality and optimize treatment processes, reducing costs and promoting water reuse. We work closely with customers to minimize discharges and support sustainability.
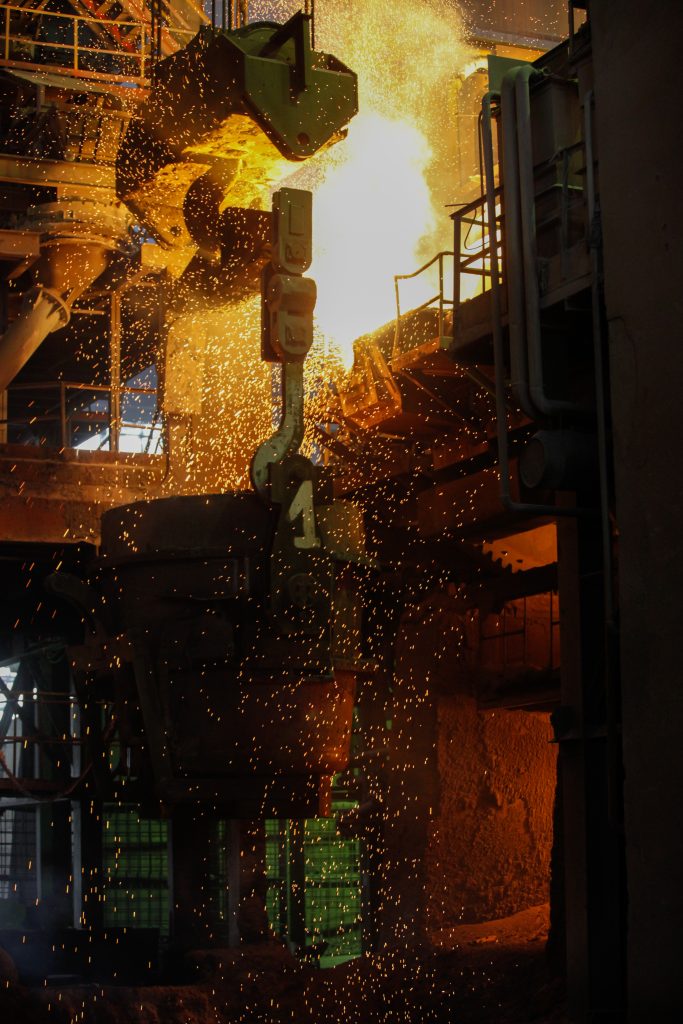
Case Studies
Steel mill saves 200.000€ in closed circuit treatment with Cetamine® Technology
Real-time KPI savings control at WPTP with S.sensing® CS
Key Industry Solutions
Aktiphos®/Ferrofos®
Aktiphos®/Ferrofos® Aktiphos®/Ferrofos® Kurita´s broad range of scale and corrosion inhibitors for open cooling systems Aktiphos® and Ferrofos ® products are designed to prevent corrosion of steel, copper and copper alloys by formation of
Cetamine® Technology
Cetamine® TechnologyDo you want to increase your boiler efficiency and lower your boiler energy consumption and CO2 emissions? Explore BenefitsMore than 5.000 treated boilers worldwideIncreasing productivity with Kurita Cetamine TechnologyCustomer
Dilurit® BC S-System
Dilurit® BC S-SystemHigh-Performance In Situ Biocide Innovative Solutions for a Better World Learn more At Kurita, we create shared value with customers and the environment. That’s why we developed our
Dust Control
Kurita provides highly efficient dust control solutions for wet spray or foam applications. The dust control solutions contain environmentally friendly suppression agents.
Ferrolin
Alberol®/Ferrolin® Sustainable cleaning with Alberol®/Ferrolin® Deposits in water systems, especially in heat exchangers may cause significant heat transfer reduction which may lead to loss of efficiency and so cooling capacity.
Kuriflock – Heavy Metal Precipitation
Kuriflock™, Kurita Heavy Metal Precipitation Technology Kuriflock™ 8603 supports coal-fired power plant in Germany to control Mercury and other Heavy MetalsKuriflock™ 6907 is used by a steel & alloy manufacturer
Kurita/Ferrosolf®
Kurita/Ferrosolf® Comprehensive treatment concepts for process applications – Kurita/Ferrosolf® Disturbances in the sequence of operation can have disastrous effects, when single parts of the equipment are fouled or damaged. Reliable
S.sensing® CS
S.sensingTM CSWastewater automation system for real-time monitoring & dosing control Innovative Solutions for a Better World Learn more At Kurita, we create shared value with customers and the environment. That’s