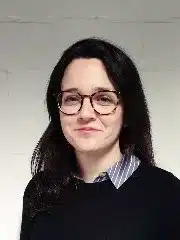
Innovation Manager CSV & Energy
New or renewable energies are energy types whose sources are characterized by the unique ability to be continuously replaced in nature. Predominant examples are Hydro, Solar, Geothermal, wind and biofuels. Those energy sources were relatively unfamiliar to the vast majority. During recent decades, their application has been repeatedly brought forward in the fight against climate change. Aligned with our role in the EU, we strive to be the first climate-neutral continent by 2050! This is an undoubtedly challenging goal. Thus, to achieve it, societies must create industries that can emit less and induce ecosystems/technologies that can absorb more.
A massive contributor to climate change is the emission of Greenhouse gases (GHG). Approximately one-fourth of this accounts for transportation (road and aviation), which is massively dependent on fossil fuels. The EU transport sector must reduce its emissions significantly to achieve carbon neutrality. This can be only realized by building a sustainable industry accounting for cleaner fuels and mobility options. One piece of the puzzle is bioethanol.
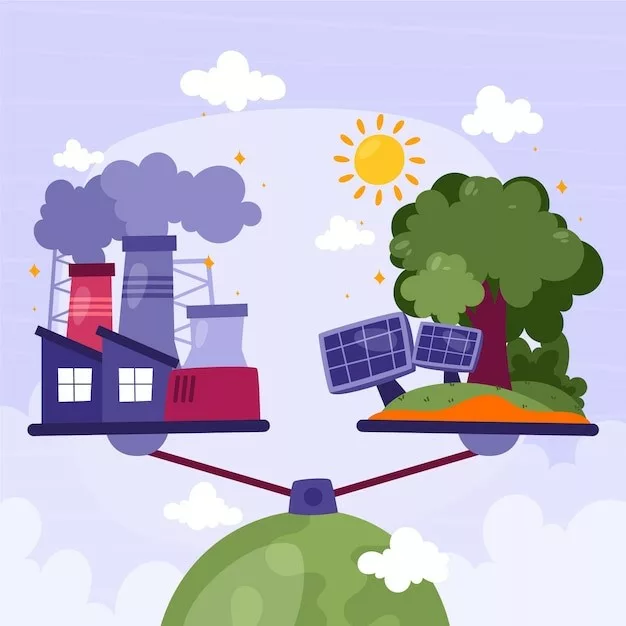
Bioethanol is a renewable biofuel produced from organic matter like corn, wheat, sorghum, and agricultural waste. It can be used directly as engine fuel or as a blend in various liquid fuels such as gasoline, diesel, and jet fuel.
It is considered “carbon neutral”, while bioethanol-combusted engines can offset the generated CO2 during the growth phase of crops. Additionally, these products can be generated locally and eliminate -to some extent- the dependency on fossil fuels.
Bioethanol production starts with the fermentation of the feedstocks. Biogenic CO2, which is the first added-value product of bioethanol plants, is produced and captured during that process. After fermentation, the mash proceeds to distillation and purification to make the final product of “bioethanol“. In this process, only the starch function is used, and the remaining product after distillation- called stillage- is still a very valuable by-product and contains proteins, fibres, and oil, which can then be processed to build dried distiller grains (DDGs) or as liquid protein to feed animals.
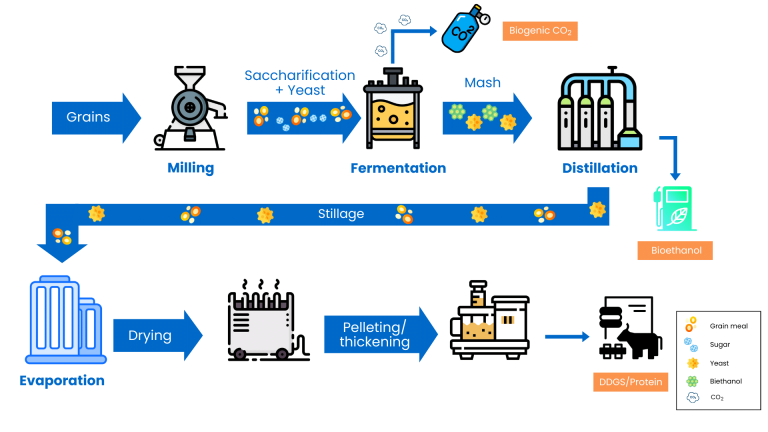
As with any other industrial application, bioethanol refineries’ production and efficiency strongly depend on the difficulties occurring in any unit. Those can include fouling, mineral deposition, and complications related to final product quality.
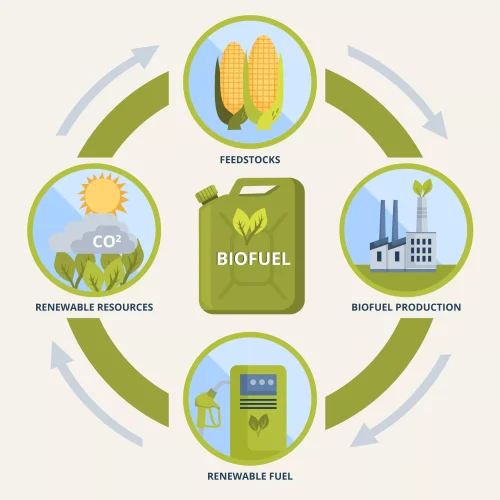
Kurita supports this industry with innovative chemistries designed to reduce air pollution, prevent deposits, and enhance fermentation and corn oil recovery to improve fuel ethanol manufacturer profitability. All our portfolios and more can be seen on our landing page.
Even though each plant has its challenges, deposit formation and fouling in evaporator systems are common issues. Oxalates and phosphates are typically observed on the surfaces, reducing heat transfer and production efficiency. Thanks to the ProHib product range, we can bring the plants to their maximum efficiency by mitigating the scale formation. ProHib product family is composed of several products. The selection of the correct ProHib is decided after the complete study of the deposit analyses done in our Research Center in Viersen.
To make the example more solid, let’s refer to the usage of ProHib 150 in a case study. The evaporator heat transfer surfaces returned to optimal condition, and the facility realized an annual cost savings of 114.000€. ProHib 150 reduced the number of CIP events for evaporators per year, significantly reducing major expenditures on CIP chemicals. With this, acid and caustic use rates decreased, positively impacting the plant water balance. From reducing acid use, residual sulphate concentrations in the co-product were also lowered, thereby improving the co-product quality. Consistent evaporator operation created more significant and more predictable oil production, strengthening the facility’s bottom line.
In conclusion, bioethanol contributes to net zero emissions and minimises dependence on fossil fuels. Kurita is actively present to support and optimize production and contribute to water and energy savings with a targeted solutions portfolio.