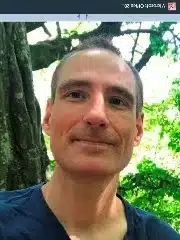
Innovation Manager Process Technologies
Dust is comprised of solid particles suspended in a gas-like air. We meet this phenomenon daily, driving on an unpaved road on a dry summer day or walking around an industrial or mining area. Dust is characterized by the type of material (e.g. sand, ores, coal, soil, etc.) and the particle size distribution, which is typically broad. Dust harms human health, especially when inhaled, and is characterized into different size fractions like PM1 (particles with a mean aerodynamic diameter of less than 1 µm), PM10, etc. PM10 is also a respirable fraction that can penetrate deep into the lungs and cause severe diseases such as silicosis by prolonged and repeated exposure. Therefore, human exposure to dust needs to be controlled and is subject to increasing regulations worldwide. On top of the health issue, dust creates safety hazards and increases wear and tear of mechanical equipment. As dust formation cannot be avoided in many cases, it is understandable that at least its’ spread needs to be reduced as much as possible.
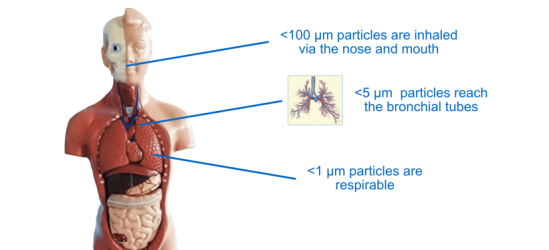
All industries handling dry, solid materials in bulk quantities know the dust issues. These are power plants, the steel industry, mining companies, construction material production like concrete factories, etc. In this article, let us focus on one of our most important primary industries: steel.
Most people know the so-called “fine dust” discussion in many large cities due to tire abrasion, erosion processes and industrial emissions. This fine dust is measured in the µg/m3 (microgram per cubic meter) range and is subject to tightening regulation. In contrast to this, dust concentrations in certain buildings of a steel plant can be several thousand times as high, sometimes surpassing 100 mg/m3 (milligrams per cubic meter). To understand the gravity of the working conditions in such areas, you need to “go to GEMBA”. GEMBA is the Japanese term for “actual place”. In a broader sense, it is where important things happen, decisions are made, or plans are realized. Many years ago, I had my GEMBA moment of dust control, walking near the sinter conveyors of a steel shop. Dust was piling up cm thick on the floor, visibility was severely impacted, and working conditions were challenging. Using a handheld instrument in preparation for a trial, I measured dust concentrations far over 30 mg/m3. Despite the obligatory protective working clothes and FFP 3 dust mask, getting all the dust out of the ears, nose, and mouth during the well-deserved evening shower took some time. Once you experience such working conditions, the need for action and improvement is apparent.
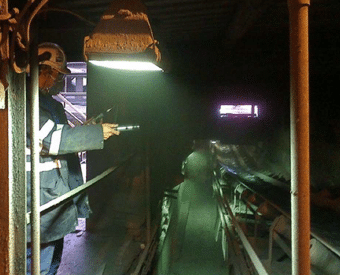
To my great satisfaction, I became one of the main contributors to our solution, which comprises a bifunctional foam product and foam spray equipment that we call the Ferrosolf foam equipment (FFE). Generally, chemical dust control spray systems can be roughly differentiated between us and foam systems. Wet sprays deliver a fine mist of a diluted product solution through a series of nozzles placed at the target location, e.g., above a conveyor belt. While known for decades and widely used, they often introduce a significant moisture level (typically about 0,5% (5000 ppm)) to be bulk material, which is detrimental to the process energy consumption. In addition, some bulk materials, such as sinter, do not tolerate such high moisture levels, necessitating a more sophisticated solution. Foam systems, in which a relatively “dry” foam is delivered with the help of compressed air and special nozzles, can achieve the same dust reduction effect as a wet spray unit while reducing the water delivery to levels as low as 0,1% (1000 ppm). Foam units are the equipment of choice whenever the process or the material does not tolerate a lot of water, or simply the energetic penalty introduced by the additional water must be minimized.
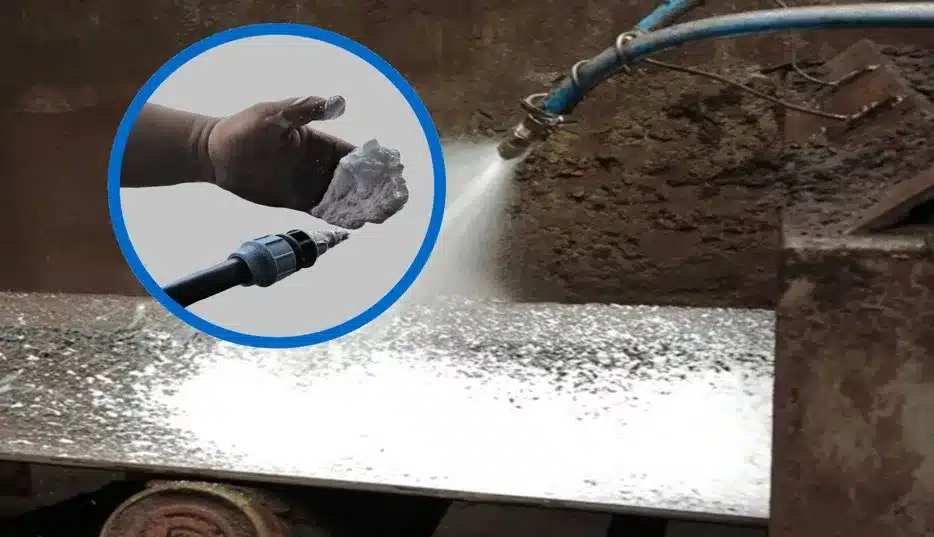
The efficiency of a properly operated dust control system can be impressive, practically eliminating visible dust where there has been hardly any visibility before
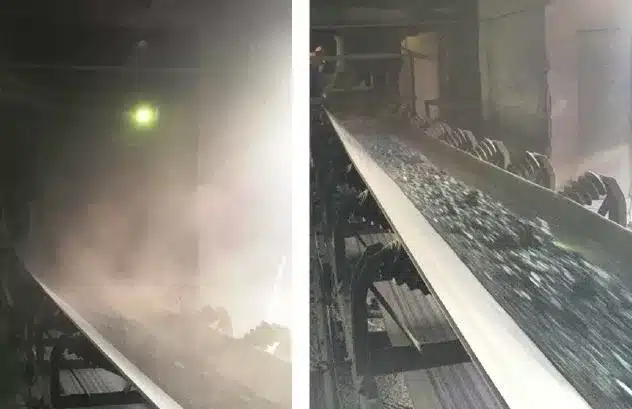
Measured dust emissions can be reduced by 90% or more.
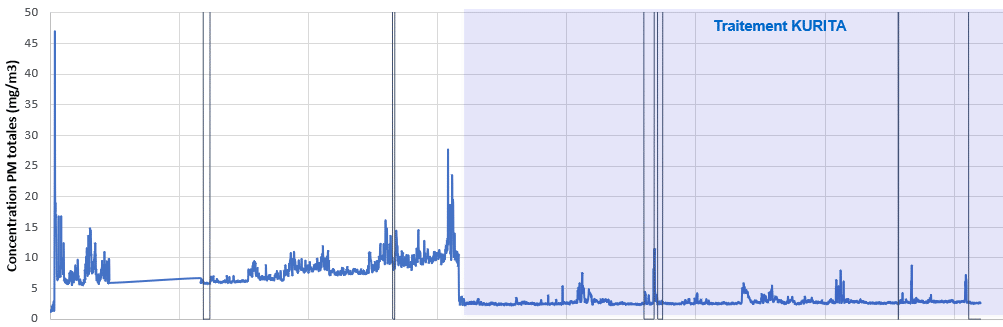
While no chemical dust control system for a large plant is exactly like another, Kurita can deliver specific foam spray systems tailored to the customer’s needs, considering the number of spray points, the desired degree of automation and other parameters. Our comprehensive dust control package includes detailed monitoring and field services.
Of course, steel plants are not the only locations where dust control is required. Bulk materials are often stacked onto huge storage piles, which can be attacked by wind, especially in coastal areas. Environmentally friendly crusting agents will provide efficient surface protection as well as ease of handling and operator safety. Unpaved roads are notoriously difficult to treat due to the enormous mechanical stress levels imposed by multiple heavy-duty trucks passing over the surface each hour, rendering traditional crusting concepts useless. In the food industry, dust control treatments must consider different aspects than heavy industry solutions, including careful raw material choice and strict regulatory limits. On top of everything, digitalization will continue its triumphant march across industries and applications, so customers are confident in demanding more advanced and automated monitoring and control systems. Whatever the challenge, Kurita is up to it!
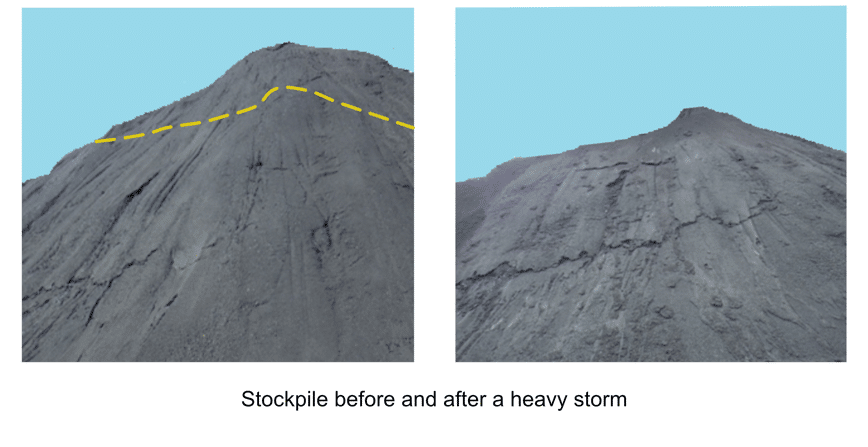